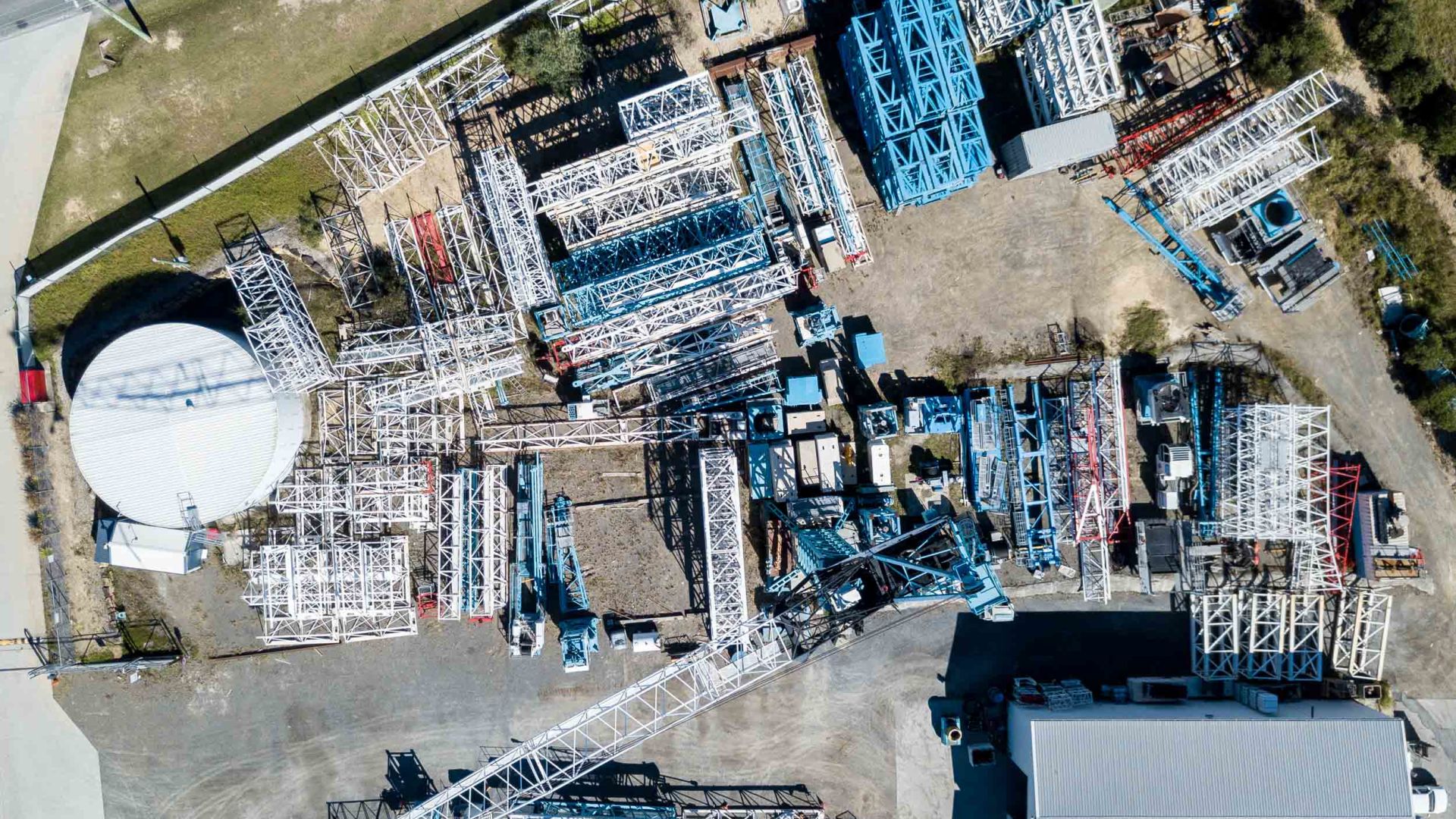
Innovative
Movement
Making possible what seems unachievable.
We love a challenge. Tight sites, rigid deadlines, unusual design, and height restrictions all impact how cranes and hoists can be used in high-rise construction. We’ve sat with clients potentially facing huge losses or even termination of projects because the constraints for cranes and hoists just seemed impossible to overcome. It’s a lot of pressure on everyone.
We stake our reputation on our out-of-the-box thinking. We work through challenges that seem insurmountable to arrive at creative solutions that change the way the whole industry approaches materials handling.
Hutchies Cranes & Hoists division pioneered the ‘crane slide’ technique, now widely used to save months on construction programs. Our novel use of recovery cranes on tight brownfield sites has transformed the industry’s approach to how these cranes are used. And our patented height adjustable tower crane system has revolutionised ultra high rise construction.
#Crane slide off lift shaft
Hutchies pioneered the technique of sliding an internally climbed crane onto steel beams when it reaches the top of the lift shaft.
With the crane temporarily mounted on steel beams sitting at 90 degrees to the lift shaft, it can then be used to retrieve the tower sections out of the shaft. This expedites the lift installation to be completed in parallel with the rest of construction. Depending on the height of the building the crane is then recovered by either the recovery crane or a large mobile crane at the end of construction. Prior to this technique, the lift installation could not be completed until the crane and tower sections were dismantled therefore adding months to program which in turn cost $$$. The solution was originally designed in 2012 for a tower refurbishment in Charlotte Street in Brisbane, taking three months out of the original construction program. It’s since been used on project like Spice, Southpoint C, Brisbane 1 and IVY & EVE.
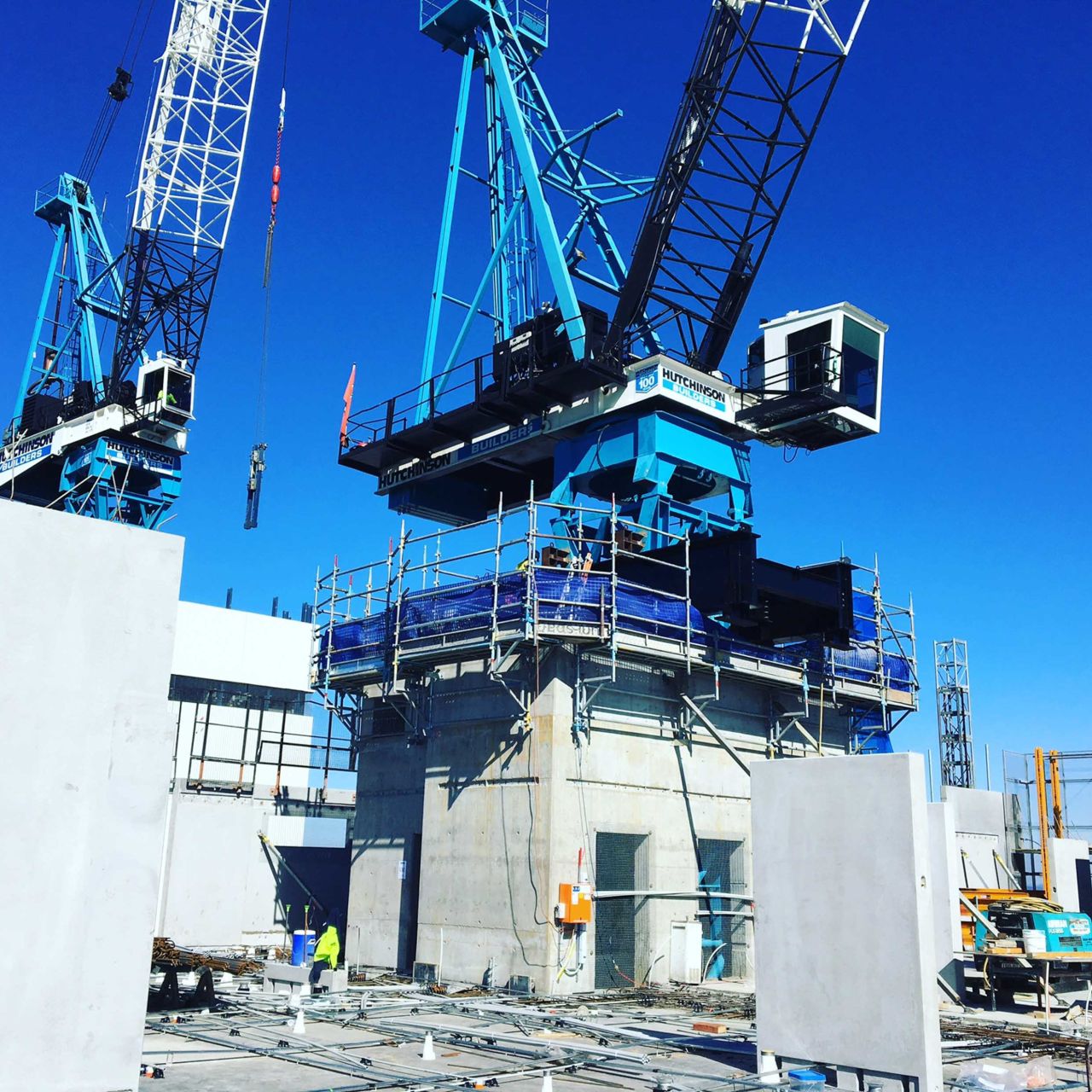
IVY & EVE, Brisbane
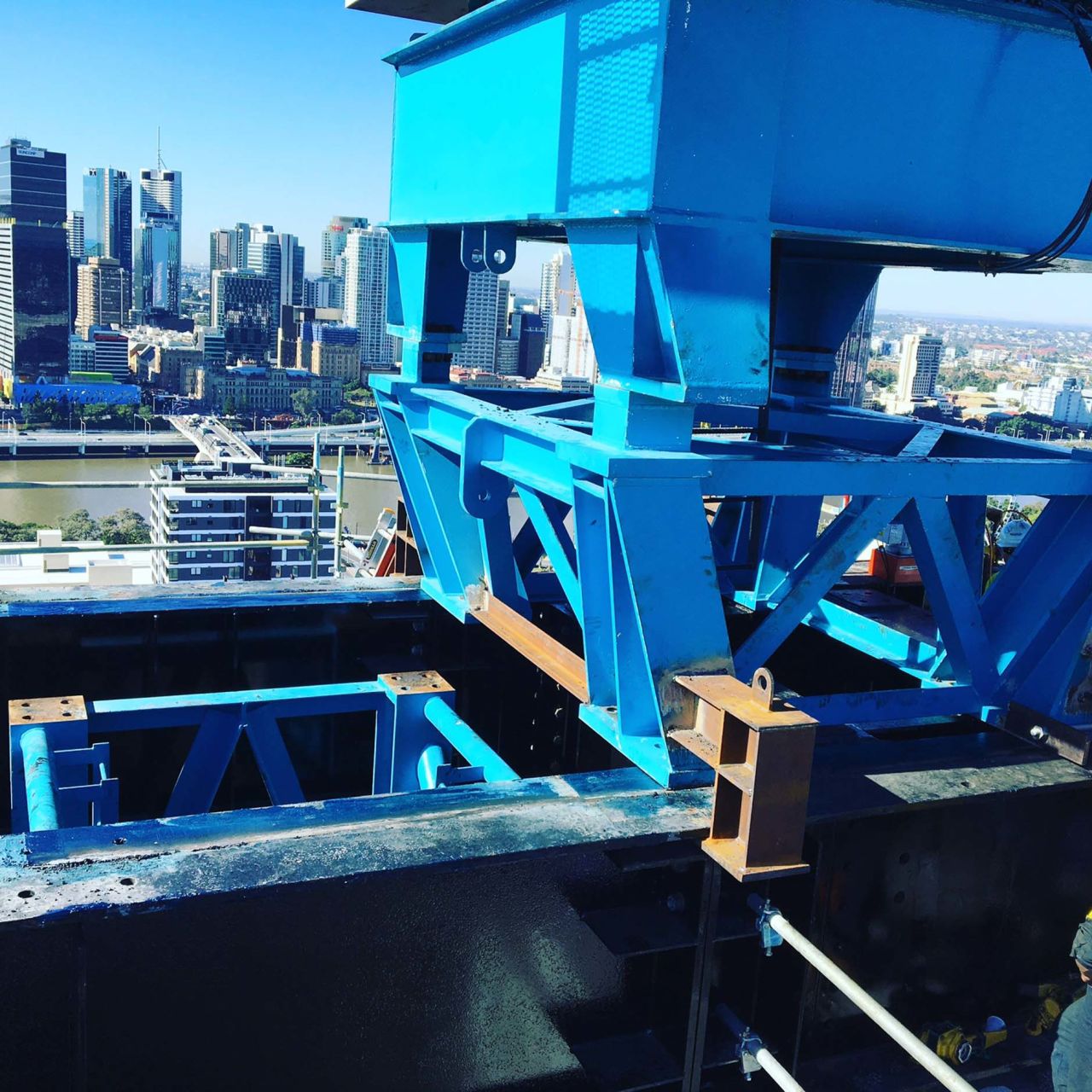
Crane Shaft Slide System
#Novel use of recovery crane
When building NEXT Hotel in Brisbane, we were faced with the situation of refurbishing an old building on a very tight site.
These constraints made it tricky to identify an appropriate materials handling solution. There was no space for a tower crane within the building footprint, and with a rear laneway only 3m wide, there was not enough space to accommodate a mobile crane. The aging building structure was not suitable for supporting the weight of a crane.
We overcame the challenge with a little out-of-the-box thinking that re-framed the way we usually use certain crane types. To retain the structural integrity of the building and address site size constraints, we positioned a smaller crane normally used for recovery on a balcony, supported by grillage. This spread the load of the crane over the strong points of the building. Given the size of the site and the building, the recovery crane was much better suited for materials handling for the project than a tower crane and ensured a safe, efficient materials handling solution.
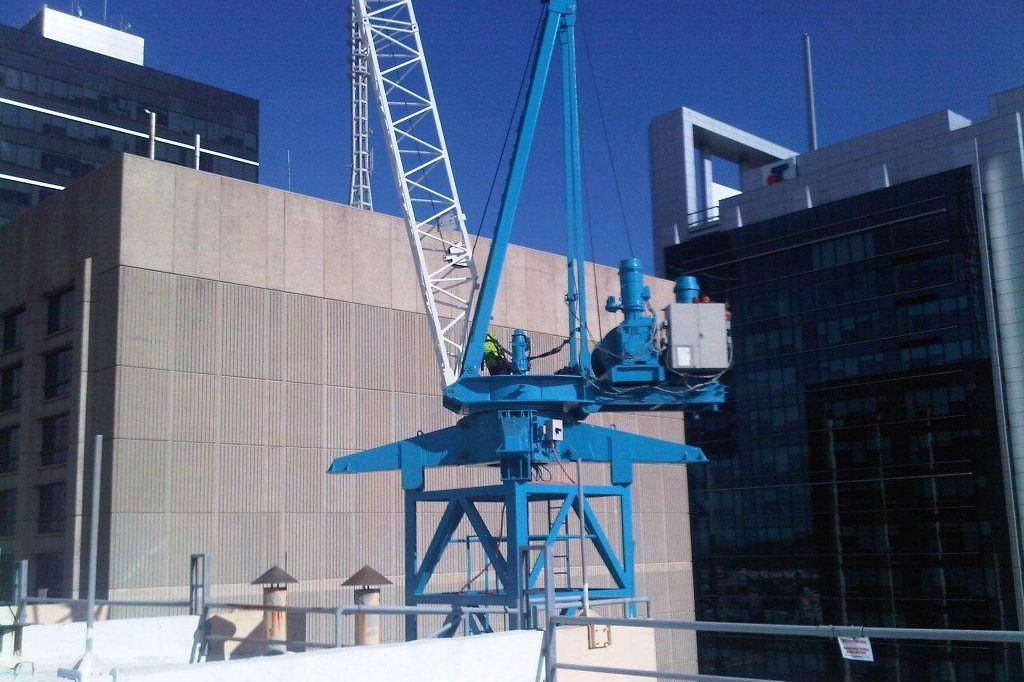
NEXT Hotel, Brisbane
#Patented height adjustable tower crane system
Our world-first vertically adjustable tower crane system has pushed the boundaries of high-rise construction previously limited by Civil Aviation Safety Regulation.
It facilitates the ability to construct a building up to 274m, which is the capped height permitted in Brisbane by the Civil Aviation Authority (CASA). The system makes it possible for builders to operate construction plant within the 12m zone permitted above the 274m height during daylight hours, and easily lower a tower crane to park below 274m at night or as directed by air authorities at short notice. Previously this would be virtually unachievable and cost prohibitive due to the constraints of traditional tower crane systems which impact upon controlled air space in the construction of ultra high-rise buildings.
Designed for the Brisbane Skytower project through a collaboration led by Hutchinson Builders, together with MBA Engineers, Building Industry Supplies (Hutchies’ cranes and hosts division), and Hutchies’ client, Billbergia, the system is comprised of three primary components:
1 / A purpose built steel tower or shaft, (internal dimensions to suit flattop crane towers), cantilevered from the side of a building
2 / A climbing tower positioned inside the static tower/shaft
3 / A three beam hydraulic climbing mechanism connected to the base of the flat top crane towers. The stability of the steel shaft and the hydraulic climbing mechanism enable the crane inside the shaft to be adjusted in a significantly shorter time than conventional methods.
The system allows the crane to be operated at up to six different heights in 4m increments, up to 24m. This provides flexibility for the crane to be moved to the specific height that it is required on the day.
In the case of Skytower, the hydraulics in the climbing system took an average total of ten minutes to push the crane up 4m and for the ram to retract ready to push to the next stage — effectively, one hour to push up the full 24m.
The creation of this system epitomises the spirit of innovation in the face of challenge. It has allowed developer Billbergia to create the tallest building in Brisbane.
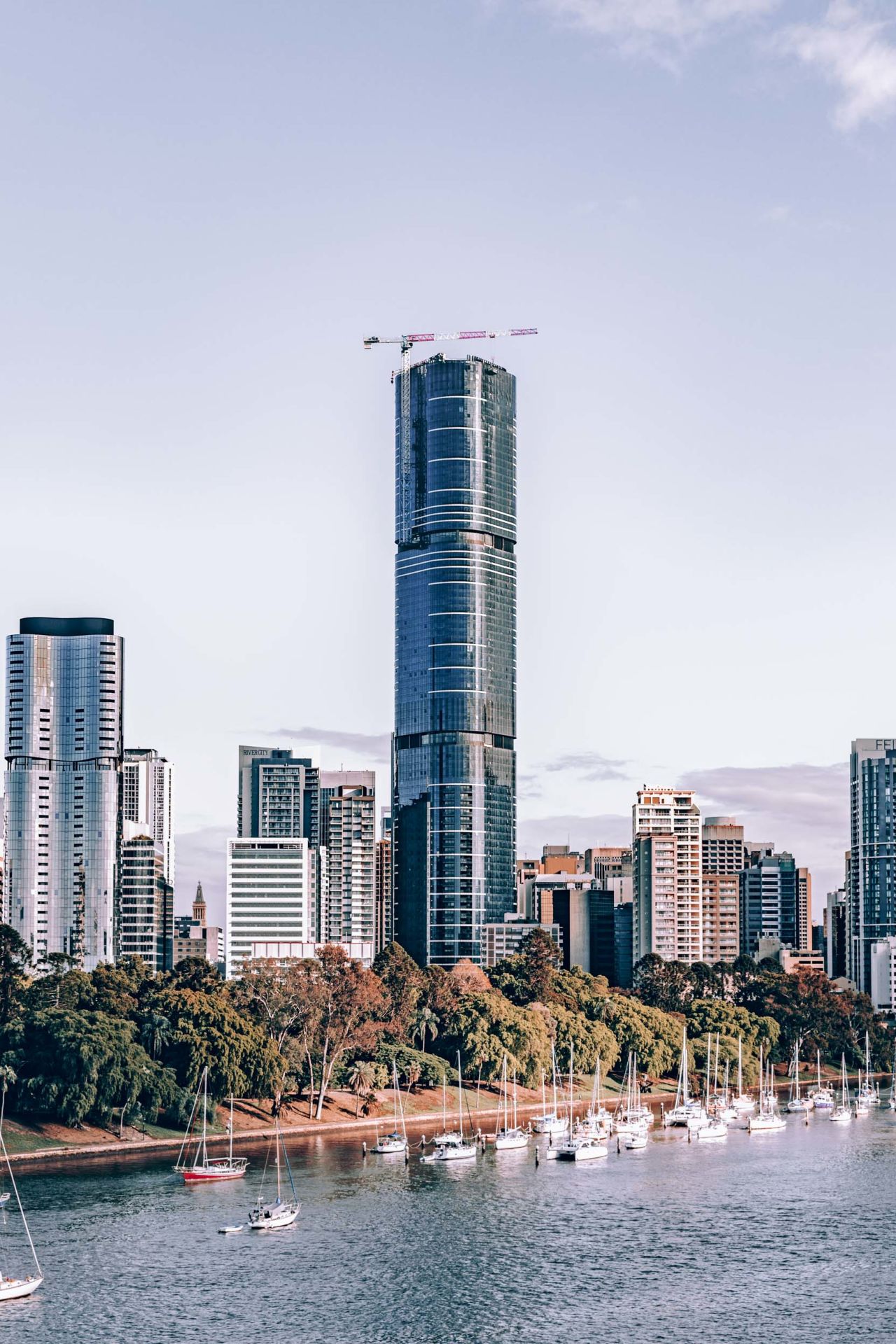
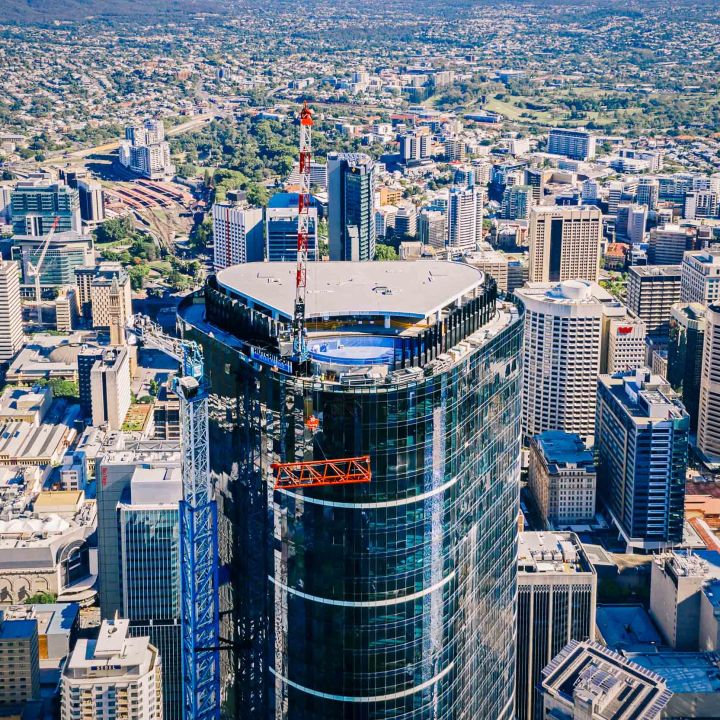
Skytower, Brisbane
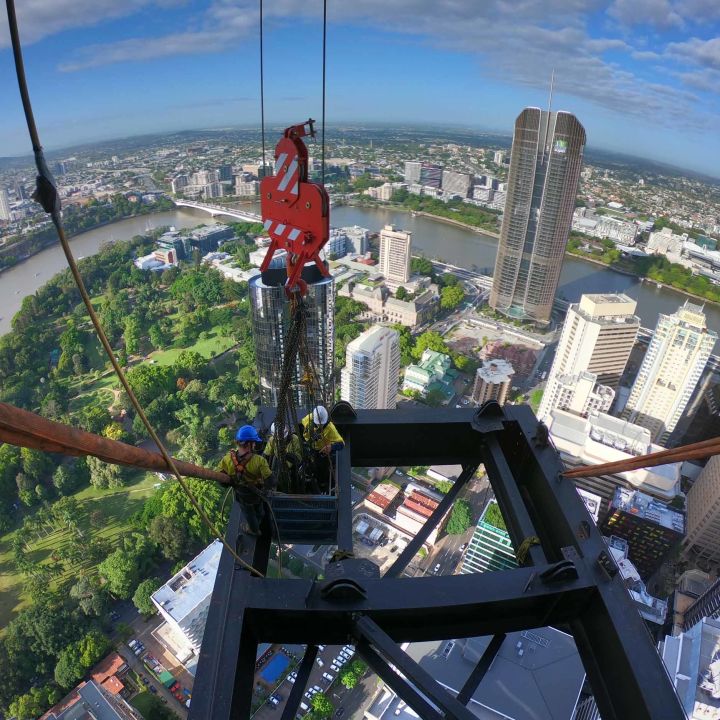
Steel Base Structure (at Level 66)
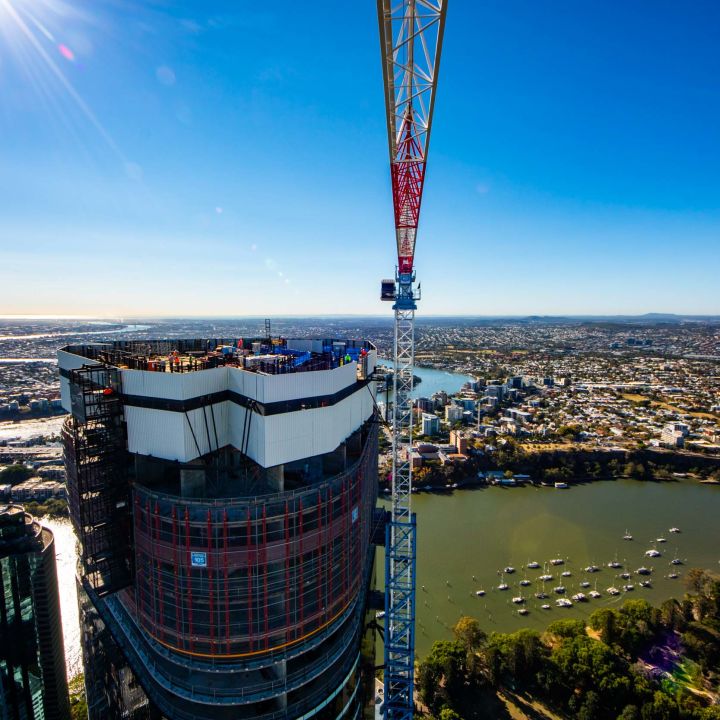
Cantilevered Tower Crane
#Multi-stage dismantling
Dismantling and recovering multiple cranes at the end of multi-storey construction can be something of a puzzle to solve.
Dismantling and recovering multiple cranes at the end of multi-storey construction can be something of a puzzle to solve. How do you get multiple cranes off the top of a very tall building? Like the rest of the project, the process needs to be safe, effective, efficient, and well thought out.
On the Brisbane Skytower project – the city’s tallest building at the time – multiple cranes were used over the course of the project, with the height adjustable system introduced part way through. The original internally climbed Favco luffing crane assembled the flat top crane and associated components of the adjustable system, before being dismantled by the flat top tower crane it had just set up. At the end of the project, a smaller recovery crane was assembled on the roof by the tower crane to dismantle the flat top. Then a further smaller ‘stiff leg’ dismantled the recovery crane, and was then broken down and taken down the building’s internal lifts on pallets.

Recovery of tower crane (at Level 90)
#Dual lifts with Franna and tower cranes
Usually mobile Franna cranes are used early in a multistorey program, before tower cranes are erected.
Usually mobile Franna cranes are used early in a multistorey program, before tower cranes are erected. They are also commonly used on smaller projects that don’t warrant use of a tower crane. Beyond these standard applications, we have used our Frannas to great effect to perform dual lifts with tower cranes for “turning up” pre-cast panels off the semi before being taken away and placed into position by the tower crane.
Pre-cast panels generally arrive laying flat on a truck. The tower crane hooks on the top of each panel, with the Franna securing the bottom for stability, assisting the larger crane to get the panel vertical so it can be safely lifted into place.
With three Franna cranes in our fleet, we are at liberty to offer more clients a pre-cast option instead of pouring each floor. This significantly speeds up the construction program and mitigates the risks of the more complicated traditional method.
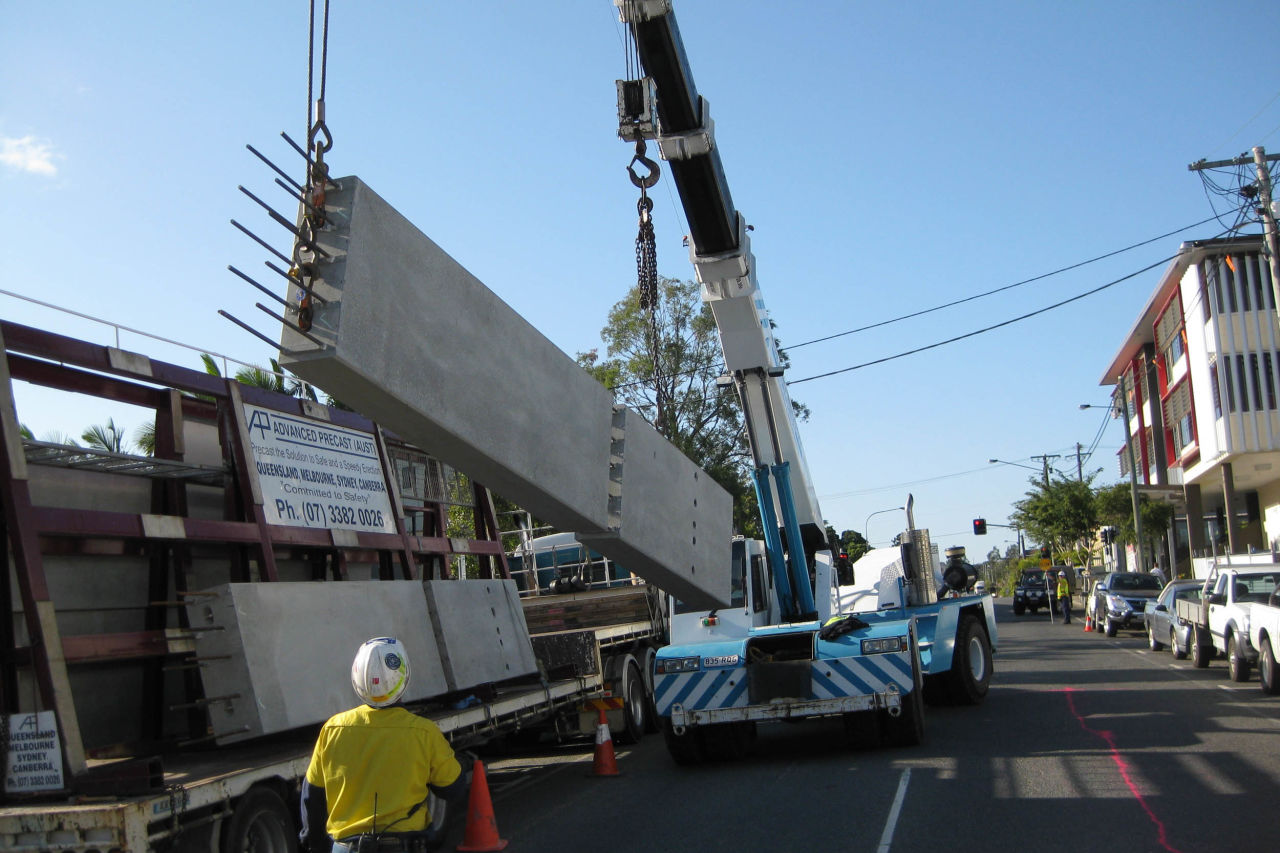
Dual lift using a Hutchies Franna crane
#Remote supply
All of our plant and equipment is readily transportable to remote locations and cities that have limited availability of gear. For example, to support the refurbishment of the historic Myer building in Hobart, we sent down one of our tower cranes from Brisbane due to the high demand for lifting gear on the ‘Apple Isle’.
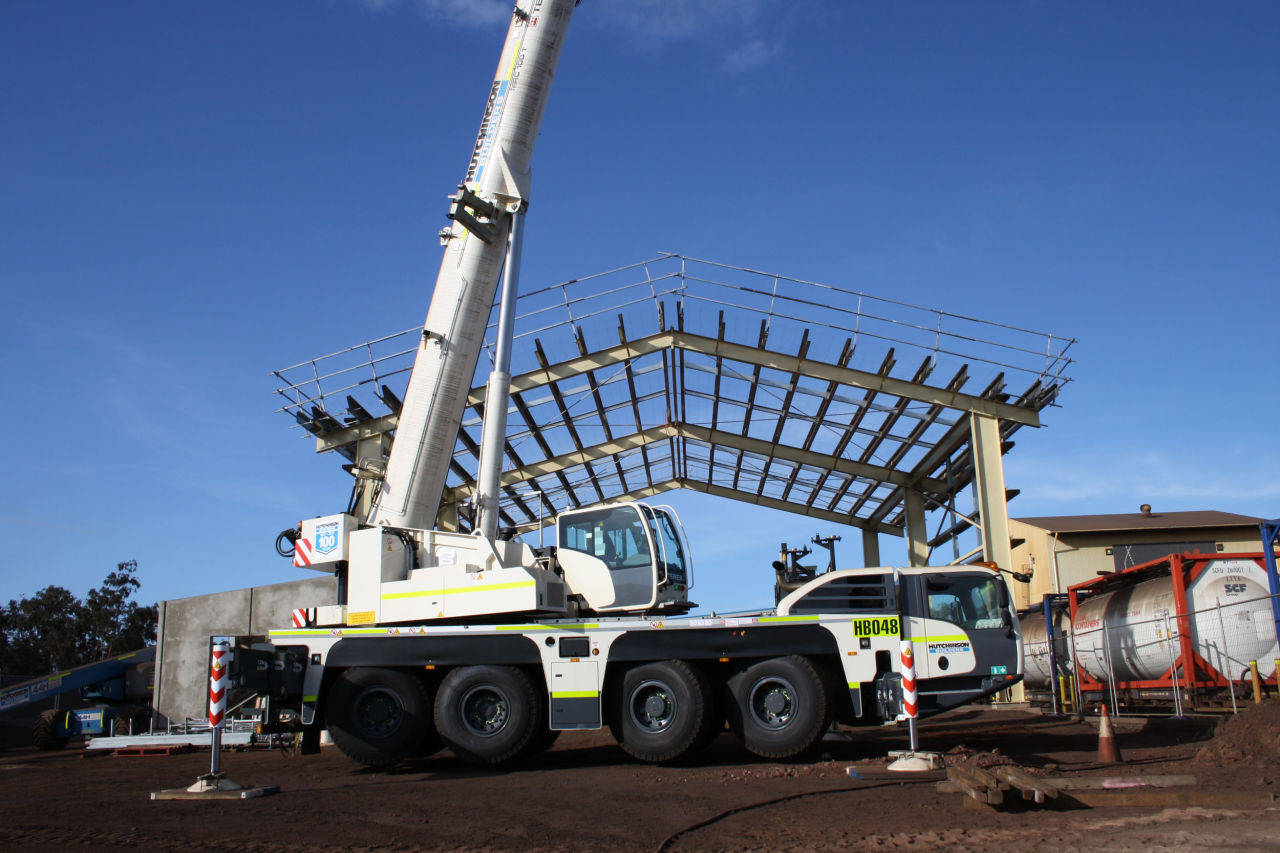
Groote Eylandt, NT
#Innovative solutions for tight sites
Modern high-rise buildings make the most of available space to maximise floorplate size and return on investment. This often means that the building footprint runs from boundary to boundary, leaving minimal options for cranes required during construction.
Modern high-rise buildings make the most of available space to maximise floorplate size and return on investment. This often means that the building footprint runs from boundary to boundary, leaving minimal options for cranes required during construction.
On taller buildings of 30 storeys or more, we can address space issues by internally climbing a crane in a lift shaft. However, for smaller buildings, this technique is not practical and would not usually be considered due to the setup cost required.
One possible approach for mid-rise buildings is to create penetrations through every floor to accommodate the crane. However, this also causes delays, plus incurs additional costs and increases potential risks from inclement weather.
It is generally not practical to accommodate a crane by positioning it outside the site boundary on a public footpath. The foundations required for a crane are approximately 7x7m2 and 1.5m deep. Building a separate foundation for a crane base would require 70m3 of concrete which would then have to be broken up and disposed of post-construction, adding considerable time and cost to the project.
On these smaller projects — like MOBO and Southpoint A in South Brisbane — we are able to devise tailored craneage solutions that utilise shared space outside the building site, without impacting safety, program, or cost.
For Southpoint A we were able to establish the footings for the crane on the footpath, so that the crane grillage was positioned above. The first tower component was placed on top of structural steel beams 6m above the ground. Pedestrians walked underneath the supporting gantry positioned over the footpath, without realising there was a crane directly above.
The MOBO development presented similar challenges, however, we had to use a different approach to Southpoint A as we were unable to use the footpath for the crane footings. Our solution was to create a void in the building to enable the crane base to be positioned in
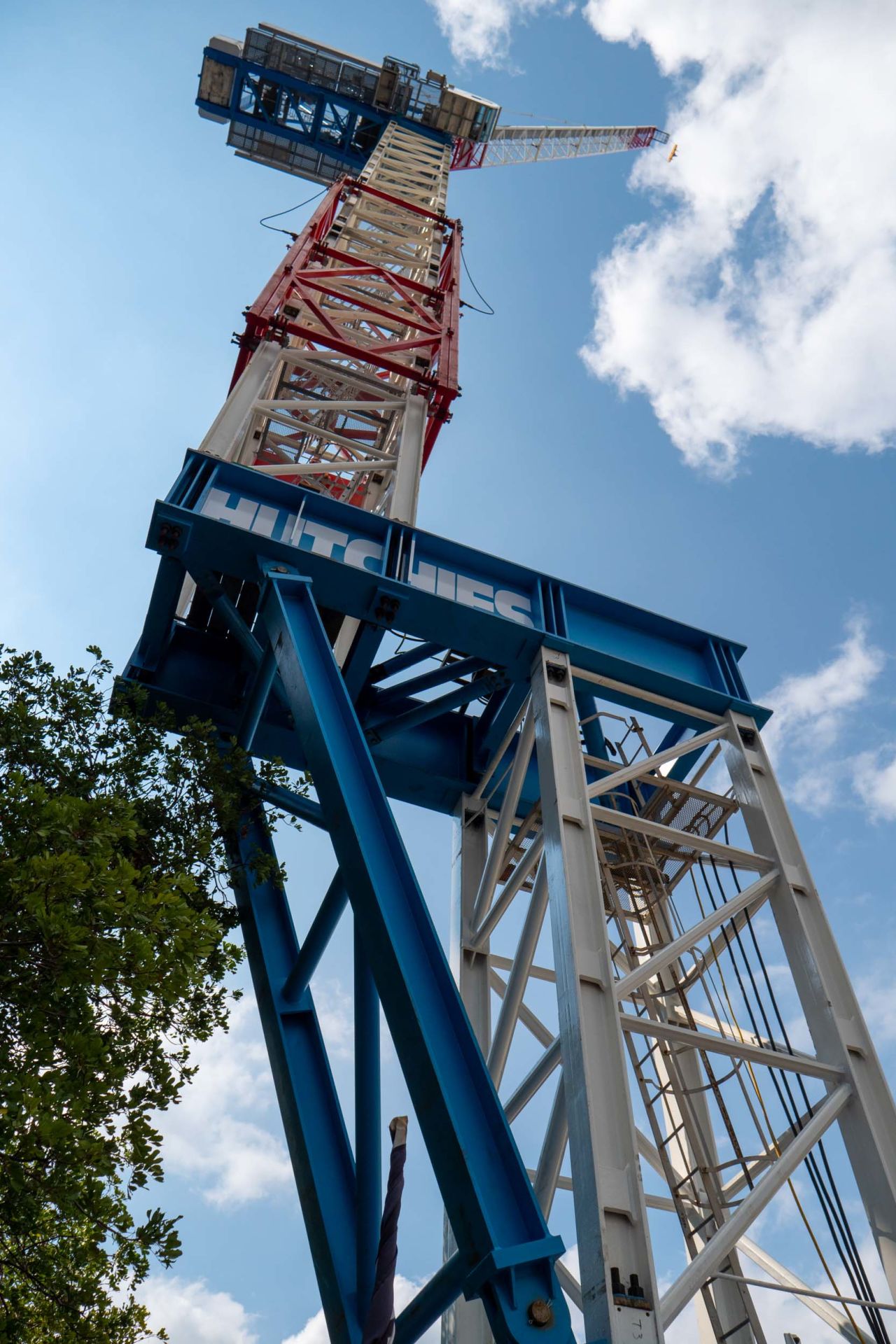
Canitlevered Tower Section
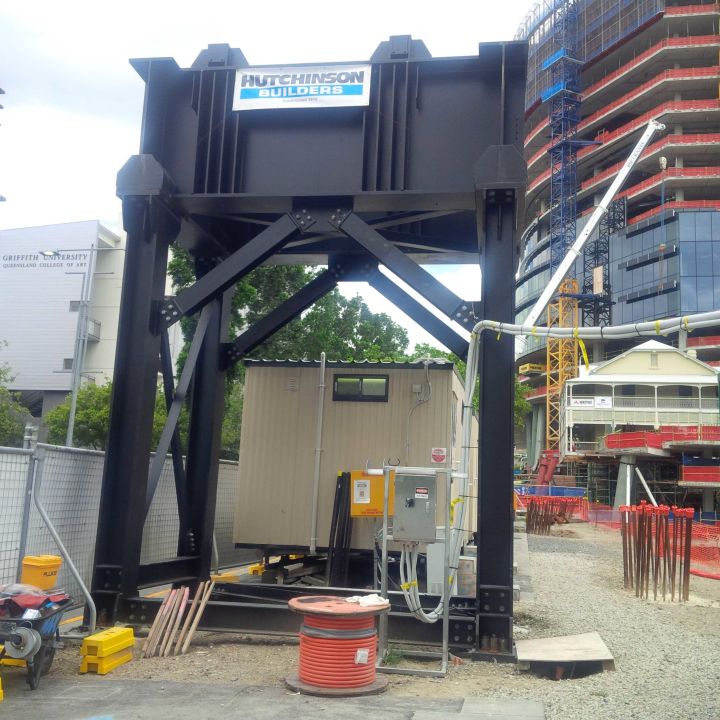
Base section
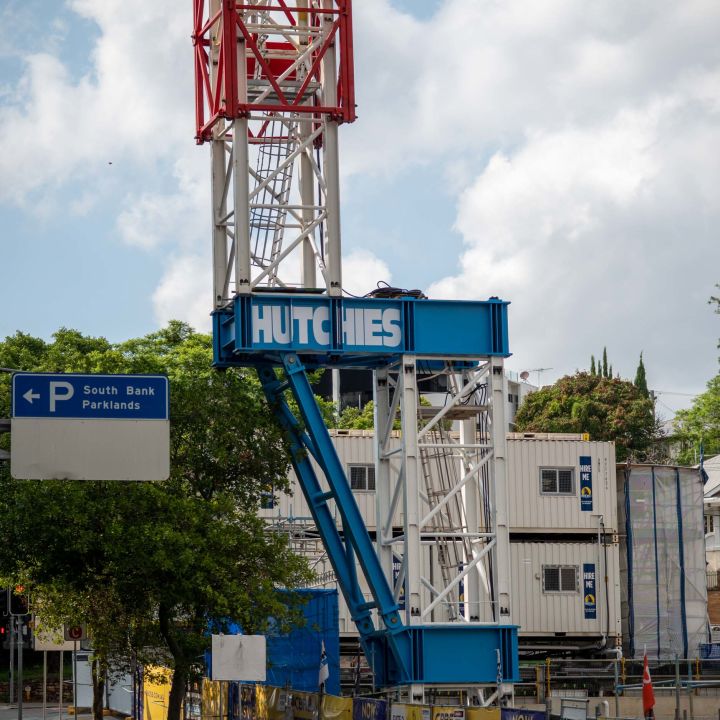
MOBO
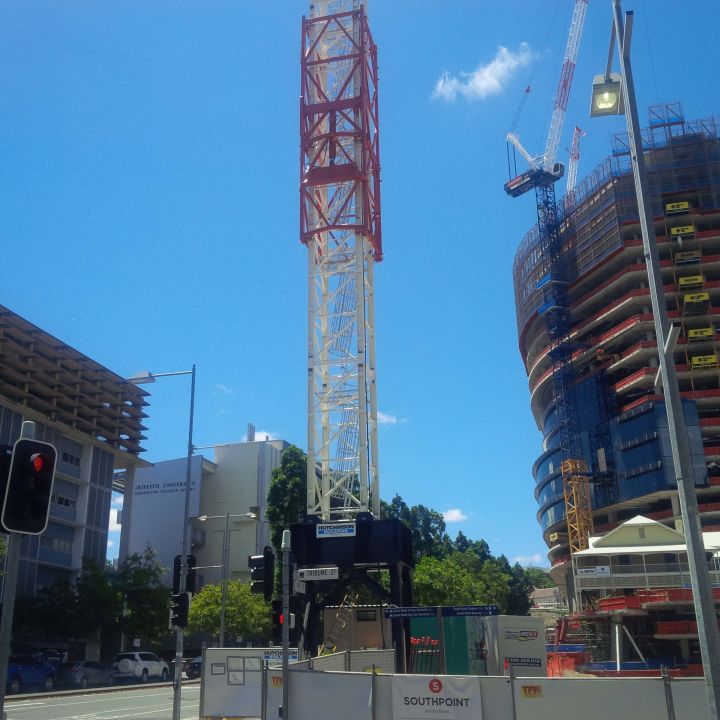
Southpoint